Floorings
Traditional flooring in the form of concrete or
asphalt that in the past have been the most commonly used may not,
in many cases, now satisfy the demands that have been placed on it.
Bitumen floorings have poor solvent resistance while concrete
floorings are easily attacked by chemicals and oils and have low
abrasion, wear, and impact resistance.
Floor coatings are widely used to overcome all
the problems that are mentioned previously and also to make the
surface easily cleanable and enable it to maintain high degree of
hygienety.
Azmeh Company provides coatings for the floor
covering of two main classes of floorings:
I- Industrial concrete floor coatings are
available in three types:
1.
Epoxy floor coating (for low mechanical loads and good water,
chemical, and abrasion resistance) EPX16.
2.
Epoxy floor coating (for medium mechanical loads, good
chemical resistance, acceptable gloss, and fast application) EPX26.
3.
Self levelling floor coating (for high mechanical loads, wear
resistance, very good flexibility, and good water and chemical
resistance) EPX06.
II- Sport Court Coating for bituminous and
concrete substrates.
I- INDUSTRIAL FLOORINGS
The technical requirements that makes industrial
floor coatings inevitable are:
1-Preservation of concrete surfaces from
abrasion which prevent dusting of concrete floors.
2-Resistance to water especially in permanent
wet areas.
3-Resistance to chemicals.
4-Providing an easy to clean substrates and
maintaining a high degree of hygienity.
5-Preventing bacterial growth.
6-The need of various colours to provide
pleasant working conditions and distinctive floor finish areas.
7-Slip resistance.
Different factors are to be considered for a
successful protection of an industrial floor such as the right
selection of the most suitable material, a proper surface
preparation, and installation by a competent applicator.
A- EPOXY FLOOR COATING (for low
mechanical loads):
Epoxy floors coated by EPX16 (two component
epoxy coating) are used in areas where chemical and abrasion
resistance are required. EPX16 is applied over primed substrates in
relatively thin layers (up to 500 microns). Typical uses are in
textile industries, chemical plants, stores and warehouses,
workshops, garages and in light industrial plants.
B-SELF LEVELING EPOXY FLOOR COATING (for
medium mechanical loads):
Epoxy floor coating (EPX26) is a good flow floor
finishing coat, used in areas not exposed to high mechanical
abrasion. EPX26 should be applied over primed substrates in
relatively thin layers (up to 1mm) to provide high chemical
resistance, good durability under foot traffic and light industrial
trucking, and an aesthetic appearance to floor surfaces.
Typical uses are in hospitals, laboratories,
food and pharmaceutical industries, clean rooms, stores, shops,
schools, industrial kitchens, canteens, showrooms, garages, and in
all industries that require moderate traffic on plant floor.
C-EPOXY FLOOR COATING (For high
mechanical loads):
Epoxy floor coating (EPX06) is a self leveling
free flowing coating recommended for areas subjected to heavy wear.
EPX06 should be applied over primed substrates to a thickness of
approximately 2 to 4mm and is considered as heavy-duty floor
covering providing a tough, skid, wear, and chemical resistant floor
covering. In addition to the aesthetic appearance that provides to
floor surfaces.
Typical uses are in abattoirs, breweries,
pharmaceutical, dairies, food and soft drink factories, cold rooms
and stores, chemical plants, battery rooms, oil refineries, and in
all industries that require heavy traffic on plant floor.
|Top|
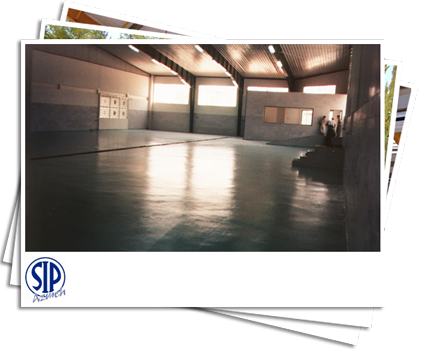
II- SPORTS COURT COATING
Sport Court Coating “WT14” based on acrylic
latex (Water base acrylic emulsion) is recommended for exterior or
interior tennis court, Basketball, handball, volleyball and other
sport courts and also for children playground, terraces, patios and
walkways. WT14 has been especially formulated to create a skid
resistant surface. It will help to weatherproof, protect and
preserve the original surface and making it more attractive and
provide a long lasting color in all climatic conditions. In
addition, WT14 is an easy to apply economical floor coating
providing exceptionally tough, flexible and durable finish.
Note:
WT14 is not recommended for use on a surface on which heavy vehicles
may be parked.
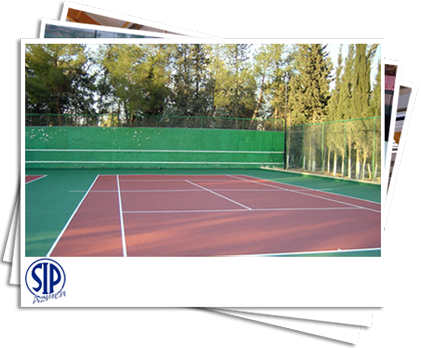
Once applied, the court coat (WT14) does not
normally require any particular attention. Cleaning can occur with
low-pressure water with mild detergent solution. In case of the
presence of any damaged area, the floor can be easily touched up by
applying one or two coats of WT14 to the damaged area, after proper
cleaning and preparation. If a renewal coat would be desired, a new
coat of WT14 can be applied directly over cleaned and dry original
coat.
SUBSTRATE TREATMENT
The right selection of suitable material for
industrial or court coating does not ensure alone successful coating
on the floor. A proper surface preparation of concrete surfaces and
installation by a competent applicator should be performed to ensure
long term bond between the concrete and the coating. Coating may
fail to stick on the surface for many reasons such as dirt or dust
is not removed during surface preparation, the surface is not dry or
too smooth, salts are present on the surface of concrete, and
finally the top layer of the concrete surface is weak.
For these reasons the surface preparation
procedure required is as follow:
NEW CONCRETE |
New concrete must be cured
at least 28 days at 21ºC with a relative humidity (RH)
of 50%, or equivalent time. Laitance, the fine cement
powder that come to the surface when concrete is laid,
should be removed by mechanical means. |
OLD CONCRETE |
Cleaning should be carried
out by mechanical means using grinding or vacuum
assisted shot blasting machine or by other mechanical
means (sand blasing). Then all dust and loose debris
should be removed using compressed air machine.
Other method of cleaning can also be used. Steam
cleaning with detergent solution is best to remove oil
and grease. Scrubbing with hot caustic solutions can
also be used to remove mineral oils and greases. It is,
however, necessary to wait for the concrete to dry out
before coating.
Concrete contaminated by animal fats should best be
removed by sand blasting or flame blasting.
A number of tests should be carried out over concrete
surfaces prior to floor coating. The moisture content of
concrete should be less than 5%. The tensile strength of
the concrete surface should be not less than 1.0 MPa and
the minimum compressive strength should be 3 MPa.
|
After cleaning of new or old concrete substrate,
fill all cracks, holes, voids, and surface damage using STOP200
prior to priming. The following tables show the different stages to
be followed when applying industrial flooring (Table 1) or Court
coating (Table 2):
TABLE
I: Industrial Flooring Systems
Epoxy Floor Coating
|
Surface Preparation |
Primer
|
Filler |
Floor
coating
|
Low mechanical loads
|
Sanding and
Stop200 (if required)
|
EPX08 (50 µ) or EPX16 (100 µ)
|
EPX55
(if required)
|
EPX16
two coats
(100-400 microns)
|
Medium mechanical loads
|
Sanding and
Stop200 (if required)
|
EPX08 (50 µ) or EPX16 (100 µ)
|
EPX55
(if required)
|
EPX26
(500-1000µ)
One or two coats
|
High mechanical loads
|
Sanding and
Stop200 (if required)
|
EPX08 (50 µ) then EPX16 (100 µ)
|
EPX55 (if required) + EPX66 (up to
8 mm)
|
EPX06
(from 2 to 4mm)
|
TABLE
II: Sports Court Coating Systems
Sport court type
|
Primer
|
Coating
|
Concrete
|
WT01 and/or SOP200
and/or Flexcoat
|
WT14
|
Bituminous
|
Flexcoat
|
WT14
|
|